MBUK Exclusive: S.170
February 22nd, 2024
You may have caught the Front Cover of MBUK on our social media this week… if you’re based in Britain it’s well worth picking up a copy of the mag (see also a review of the A130 and a Welsh trail builders piece featuring Dan) but for those of you outside of the UK we thought you’d like to catch up on the Sneak Peek into the soon to be released S- range. Here’s some excerpts from the feature…
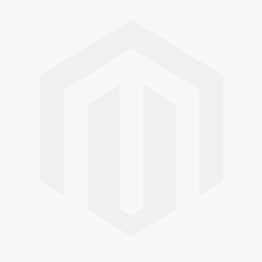
MBUK: Atherton Bikes had an amazing 2023, with Rachel Atherton’s triumphant return to racing, team rider Charlie Hatton being crowned world champ, the brand’s 500th sale and the launch of the benchmark-setting A.130. The main thing holding them back has been the cost of hand-building bikes from titanium and carbon fibre – so, they’re releasing an alloy range, and you’re the first to get a look!
“Right from the launch of the bike company five years ago, we had this vision for a more accessibly-priced range,” says Atherton Bikes co-founder Dan Brown.
“We wanted to bring all the great stuff we’ve learned from our ‘halo’ range to the core MTB riders, the people we see at Dyfi Bike Park every weekend. To make a strong, durable, high-quality ride that would be in reach for a lot more people. All the characteristics of the A-range – perfect fit and geometry, playful ride feel – will be carried through into this new S-range, but rather than titanium and carbon fibre, we’ve used aluminium.
The ‘S’ in the name stands for subtractive manufacturing (removing material), as opposed to the additive manufacturing (3D printing; building up material) used to create the ‘A’ range bikes. The new range will still use lug-and-tube construction, but instead of carbon tubes joined to titanium lugs, it’s 100 per cent aluminium. The lugs are made for Atherton externally using an innovative application of CNC machining and frames are built in Atherton HQ Machynlleth “Building in-house is important to us,” says Dan. “Partly because it gives us greater quality control, and partly because we’re so passionate about helping to develop this fantastic area we live in.”
As well as giving the bikes a unique look and utilising the knowledge built up over the past five years, lugged construction allows the brand to use 7075 aluminium, which has much higher fatigue performance and ultimate tensile strength than weldable alternatives such as 6061.


The bike pictured is a final prototype. Dan Brown said “We’re getting ready to start production and are agonisingly close to being able to launch our online sales.This one’s been a long time in the works, and everyone’s really excited, it’s been a passion project for all of us. Most of the testing has fallen to Dan, the design and engineering team, and the dig crew, so it’s fair to say it’s been thorough!”
5 KEY CHANGES:
1. The new bikes will still be built in Wales, using lugged construction, but from aluminium rather than carbon and Ti
2. ‘S’ stands for ‘subtractive manufacturing’ – the lugs will be CNC machined, not 3D printed
3. Dave Weagle’s DW4, a simpler – but tried-and-tested suspension design means less adjustability, but also less workshop time
4. There’ll be 12 sizes – fewer than the 22 standard sizes plus a custom option offered for the ‘A’ bikes, but still more than pretty much anyone else offers
5. Atherton Bikes will be releasing a full range, launching each model individually throughout the year