Built Different: If Gee Atherton made bikes...
November 14th, 2023
The physical and mental strength of the Atherton siblings has near legendary status in the mountain-bike world (in no small part due to Gee’s stunning big mountain projects and spectacular crashes). Here, Atherton’s Head Designer Rob Gow talks about how this particular character trait informs how every Atherton Bike is designed and built.
RG: Given the uncompromising standards and the toughness (in both body and mind) that Dan, Gee and Rachel are known for, it’s no surprise that the products they put their name to would share those super-strong characteristics. With founders this strong in their character and outlook it’s obvious to me that a similar vibe quickly passed into the team to inform all our design decisions.
An Atherton bike was never going to be generic, it looks different, it rides different and it lasts different… which given the punishment that the founders dish out on a regular basis was always going to be a key driver…It was a match made in heaven for an engineering team used to the perfectionism demanded in aerospace and F1 to bring their experiences into the bike industry.
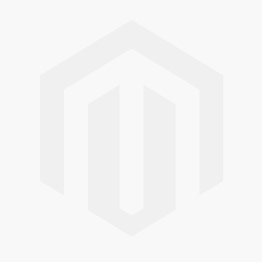
Robustness and durability are always to the fore. There’s a hierarchy in sustainable design based on how much energy and material you can retain; the highest level of that hierarchy deals with how you can extend the usable life of a product … that’s true sustainability. I’d describe myself as a climate activist so achieving real improvements in this area is very close to my heart. Our objective was unanimous, engineers and riders committed to create bikes that people will be stoked to ride for a very long time.
Right from the start, strength was high on our agenda – in fact Dan Atherton often says that seeing riders push the envelope of what could be done on a bike at Red Bull Hardline (with bike technology not really keeping up with that level of progression) was a catalyst for him wanting to start the company. After a couple of years of getting comfortable at the event, riders were starting to demand more from their bikes; away from the cameras there were plenty of frame failures putting those riders at risk. Dan wanted to start a company that would push bike manufacturing technology as hard as Hardline’s world-leading competitors were pushing the riding…
For all three siblings, years of not getting through a whole World Cup season with all frames intact was a problem waiting to be solved. From our very first conversations strength was key, in fact Athy’s failure to break our prototype test bike (a fore-runner to the Athertons we produce today) allowed the siblings confidence to invest their time and money in an admittedly left-field approach. The first time Gee rode that test bike while the founding of a bike company was still under discussion he deliberately launched out of a berm at the top of racetrack to land to flat on the fire-road … the bike was totally unaffected by the impact. Knowing Gee as I do now, I think that probably went a long way in helping to seal the deal!
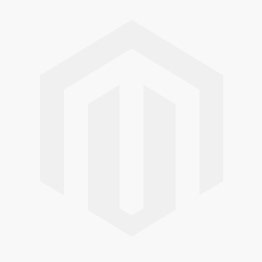
There are some strong engineering principles behind the strength of our bikes.
Composites (such as carbon) work really well in simple shapes and with simple loads and metals work well in more complex shapes and where loads are multi-directional, for instance around the bottom bracket or the Headtube. On our AM bikes, we take the best of titanium, apply it where it performs best, and combine it with high-stiffness carbon tubes (from a company that makes the best yacht masts in the world!). The trick is to ensure you don’t offset those benefits through the weight of the joint. We use double lap shear joints, a proven technology which our design and engineering team were very familiar with from stints at Airbus and Renault F1. It is a very weight-efficient way of creating a joint. When you join materials it’s really important to be aware of galvanic corrosion, certain combinations work a lot better than others, but the relative positions of carbon and titanium in the Galvanic Series means that they bond really well, then the natural surface finish of our AM printed lugs is quite coarse, rough textures are great to bond.
Traditionally where materials are joined is a point of relative weakness so in our design for strength we’ve also moved the location of the joints away from the areas of highest stress...
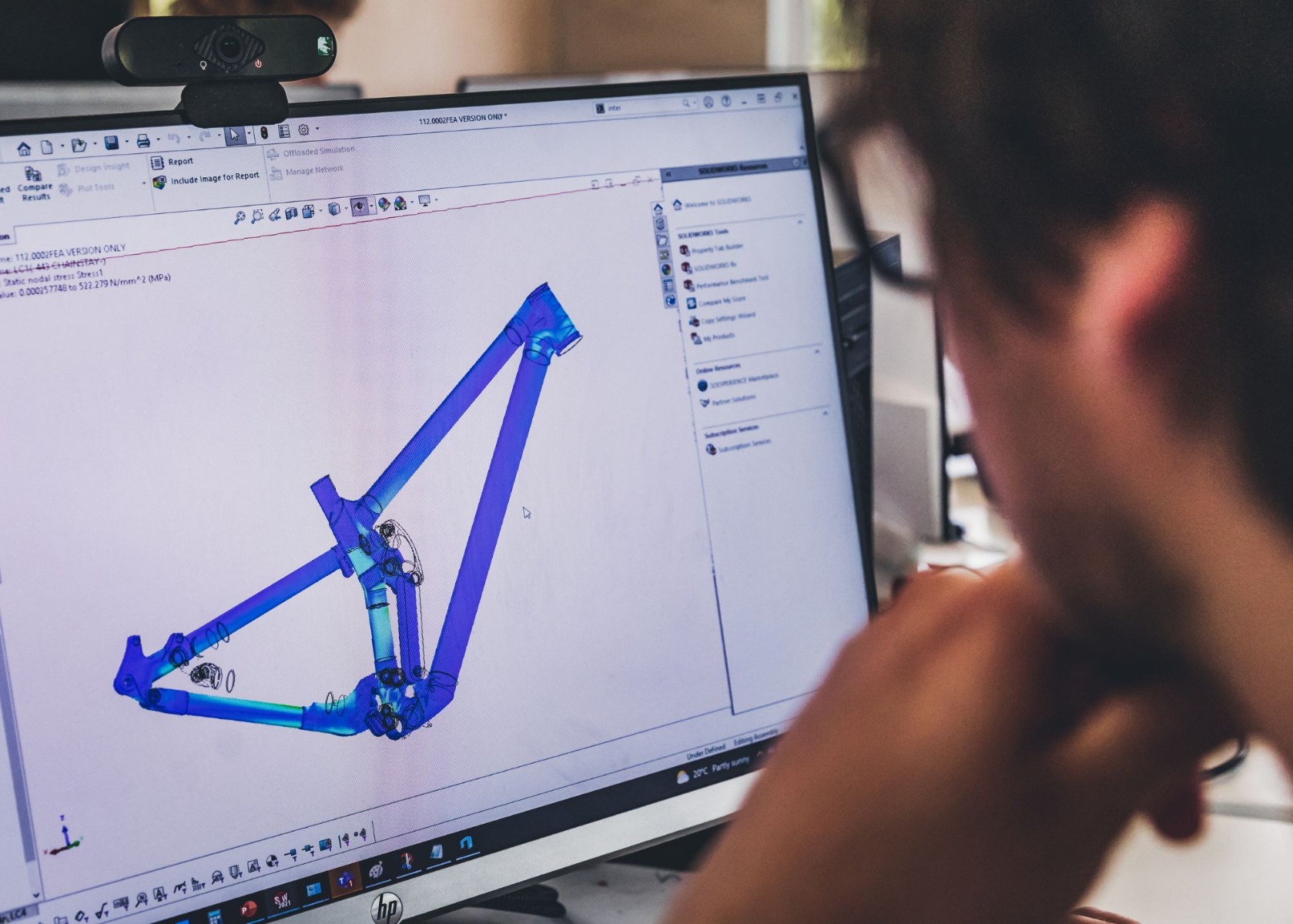
The frames are developed using the principles of infinite-life design for the metal elements and no-growth principles for the composite elements to ensure strength and durability. We use a mathematical approach called Topology Optimisation to refine material layout meaning that we can provide the lightest possible design for a given set of loads and boundary conditions while avoiding fatigue. We test by applying DH load cases to all our bikes, so for instance when we’re testing the carbon we can saturate the composites in barely visible impact damage, replicating stone knocks etc, all those inevitable little impacts, but we can apply those load cases indefinitely to the tube in that impacted condition and it will be ok.
Given the high level of requirement that we set, it’s often a surprise to people that our frames don’t turn out heavier than a moulded carbon frame, we’re actually somewhere in the lighter end of the field…they are not the lightest because our bikes are designed to be ridden hard!
Every model is validated using a test-pyramid approach, materials are first tested in the lab, bonded assemblies are evaluated and the whole bike is re-tested at EFBE in Germany. Their Tri-test standard is world-leading, but for us, they devised a special set of tests, cherry-picking all the most rigorous elements from Cat 4 and Cat 5 for a super-test ( or example in Cat 5 which is Downhill the impact tests are more demanding to simulate big drops, in Cat 4 ( Enduro) the fatigue loads used are higher … the bikes passed these worst-case scenarios with flying colours, even more, impressive when you compare our test bike (post 6 months of Dan Atherton’s hard use) with some of the bigger brands who send a brand new frame for each individual element of the tests… And of course, we let Dan, Gee and Rachel and a whole squad of Dyfi-based staff do their worst to every prototype. So even our 130 trail bike has a lifetime warranty including Bike Park use.
And if lab-tests don’t really do it for you, consider the fact that Gee’s AM200 survived that horrific crash at the base of a 75-foot drop with only the smallest of scratches … it’s in the shed right now waiting to be ridden again.
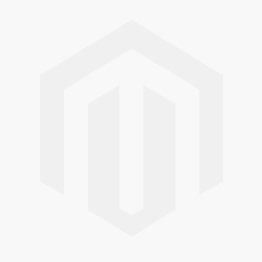
I view what we do as honest design, honest engineering with some strong guiding principles and an aesthetic driven entirely by performance.
Those principles also inform the work on our new, aluminium range of bikes the first model of which we hope to launch very soon. Most weekends you’ll find half of the team riding at Dyfi Bike Park and the number of cracked frames and warranty claims we see or hear about on the uplift is absolutely heart-breaking.
So we took a fairly conservative design approach to this new range to ensure maximum durability … and of course, subjected it to some very aggressive testing … more detail on that in a couple of weeks’ time, but for now I can just share one of the real challenges you face as a designer and an engineer is that you want to test your product until it breaks (so you can improve the weakest link ) … but ever since the second prototype that’s proved impossible. We’ve tried pretty damned hard but we’ll just keep on trying…