Blog
90 Foot Gaps and 100% confidence on the A.200
06 June 2024
10th Red Bull Hardline
June 2024
Last week we watched the spectacular 10th anniversary of Red Bull Hardline, Wales.
The event is designed by our own Dan Atherton and has become known as the world’s toughest test for both bikes and riders.
It’s the ultimate demonstration of skill, strength and quality, but underpinning the jaw-dropping features is some serious science.
We spoke to Hardline veteran and co-founder Gee Atherton, and to Marcus Schröder, of EFBE Germany, the leading bicycle test laboratory since 1995 – in very different ways both of these men have tested the A.200 to the absolute limit …
2 Sides of the same coin
From the first secret meeting in 2014 to the 2024 races in Tasmania and Dinas Mawddwy, Dan Atherton’s goal for Hardline has been to showcase the wildness, the intensity and the ever-higher level of accomplishment in downhill mountain biking. The event breaks down barriers between DH racing and freeride, pushing riders to their limits and progressing the sport as a whole.
It's easy enough to trace the growing level of confidence (consider the step-up and Kaos Seagrave’s 2019 race run back-flip) and it’s that progression that motivates Dan to keep building bigger, better more exciting courses, never more so than in 2024.
Of course, if you’re pushing riding to its limits you’re also pushing bike technology to its limits, there have been many times throughout the event’s history when riders demanded more from their bikes than they could give; more than one occasion when frame failures were swiftly moved out of range of the cameras.
Dan often says that seeing bike technology not keeping up with rider progression was a big catalyst for him wanting to start Atherton Bikes; a company that would push bike-manufacturing technology as hard as the competitors were pushing the riding. Our A.200 has been part of some spectacular crashes over the past 5 years at the race, not least this year under Atherton test rider Jim Monro, but it remains unscathed.
This year, following a crash at Red Bull Rampage last October, Gee wasn’t far enough into his recovery to be allowed to race, but he was determined to be part of the testing crew … motivating the other riders and showing off the A.200 on the world stage …
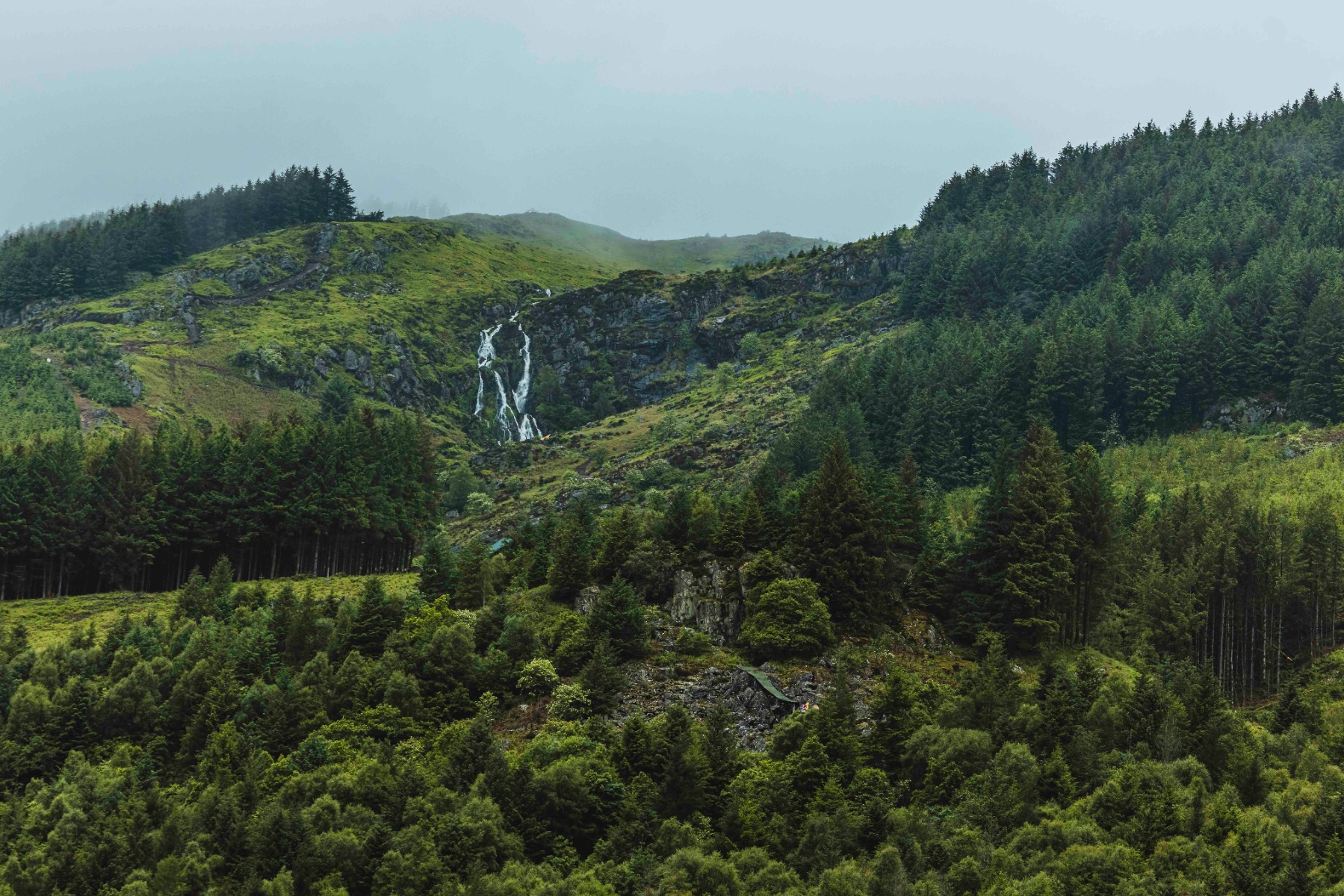
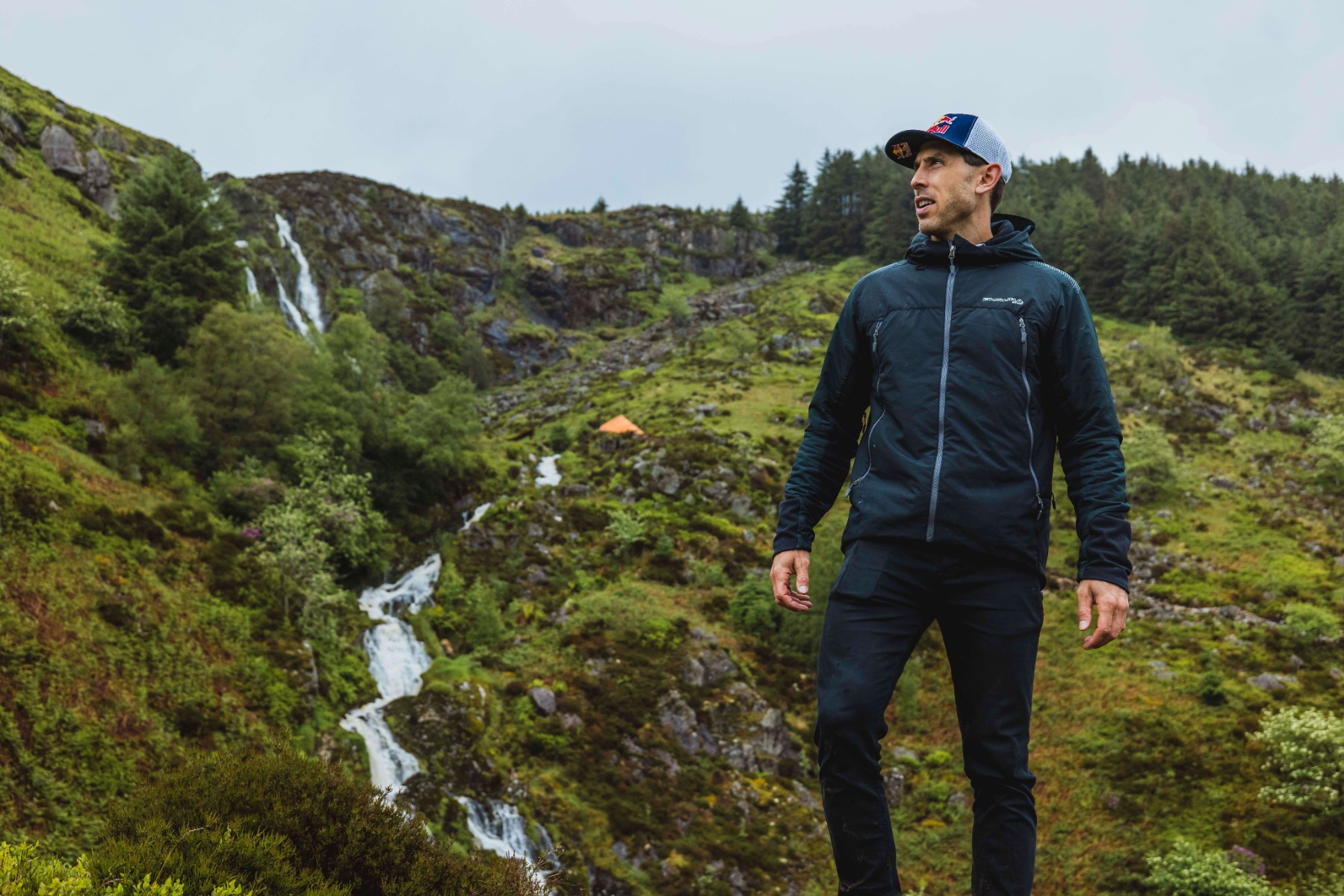
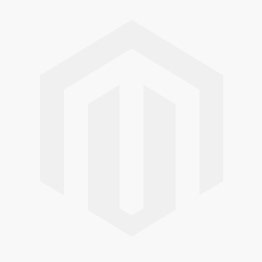

Gee Atherton - Hardline test Rider
Gee said “Wanting to ride Hardline this year was a big driver for me during the recovery process and I have been aiming at it for a long time, but I knew it would be difficult. It was always going to be hard to be ready in time but I knew I was up to the challenge, I wanted to be part of the crew testing what we had designed.
When they talk about this event, people talk a lot about bravery but to me, it’s not a case of being brave, it’s more just knowing what myself and the bike are capable of. I know I can ride Hardline quite confidently.
Testing features is something I love, the challenge of building, designing and riding something new is huge. Some people talk about us doing things that are too risky, or pushing it too far and from the outside, of course, it’s going to look like that, but when you are doing new things and testing limits, they’re judged “impossible” at first and then, once you have done them, they seem easy.
I enjoy pushing myself to the limit of what I know I can do, and I would never be able to be in this position, if I didn’t 100% trust the bike, if there was any doubt as to whether it would survive, you could not put yourself in that position it would be too dangerous. The question of whether the bike is going to work and be strong enough, since the very start of Atherton Bikes it’s never entered my mind, from the beginning strength has been an absolute priority.
How does the EFBE process work when testing Atherton Bikes?
"For me having the EFBE tests is amazing, it’s an extra seal of approval, another layer of confidence, and of course, it helps people outside of this immediate company to be reassured. But to be honest we already knew that the bike was going to be up to it, (the frame passed with flying colours). The engineers we work with here at Athy Bikes have proved themselves to be so knowledgeable in this area, over the years, we have both understood what the other ones are capable of, and we’ve learned to trust each other. I know those guys are going to design a bike that is going to take some of the biggest hits in the world in its stride.
Before we even ride a prototype every model (including the A.200) is validated using a test-pyramid approach, materials are tested in the lab, bonded assemblies are evaluated and then the three of us Athertons, the team riders, the dig crew and the Athy bikes staff all get to thrash the bike at Dyfi Bike Park for a couple of months, only then is the frame tested at EFBE.
We chose to work with these guys because their Tri-test is world-leading, and much harder to pass than most, which suits us of course, we never take an easy route! But for us, they devised a special set of tests, cherry-picking all the most rigorous elements from Cat 4 Enduro and Cat 5 Downhill for a combined “super-test.”
It was really interesting to see that in Cat 5 which is Downhill the impact tests are more demanding to simulate big drops, while in Cat 4 ( Enduro) the fatigue loads used are higher … of course, our bikes passed these worst-case scenarios easily.
On the surface there’s not much common ground between the highly scientific approach of a German test lab and the testing that we do at Hardline – for example, EFBE tests far exceed any national and international safety standards so I guess you’d expect a level of conformism with that but there is a rebellious streak to them too! Marcus told us that EFBE came to life when 4 engineers met at Aachen University in the late 80s and one of them (Manfred Otto) proved in the course of his PhD thesis - that the test method for bicycles his boss had dreamed up didn’t work at all! Not a smart career move, but that started the development of some of the force-controlled fatigue tests which still form the basis of the EFBE TRI-TEST"
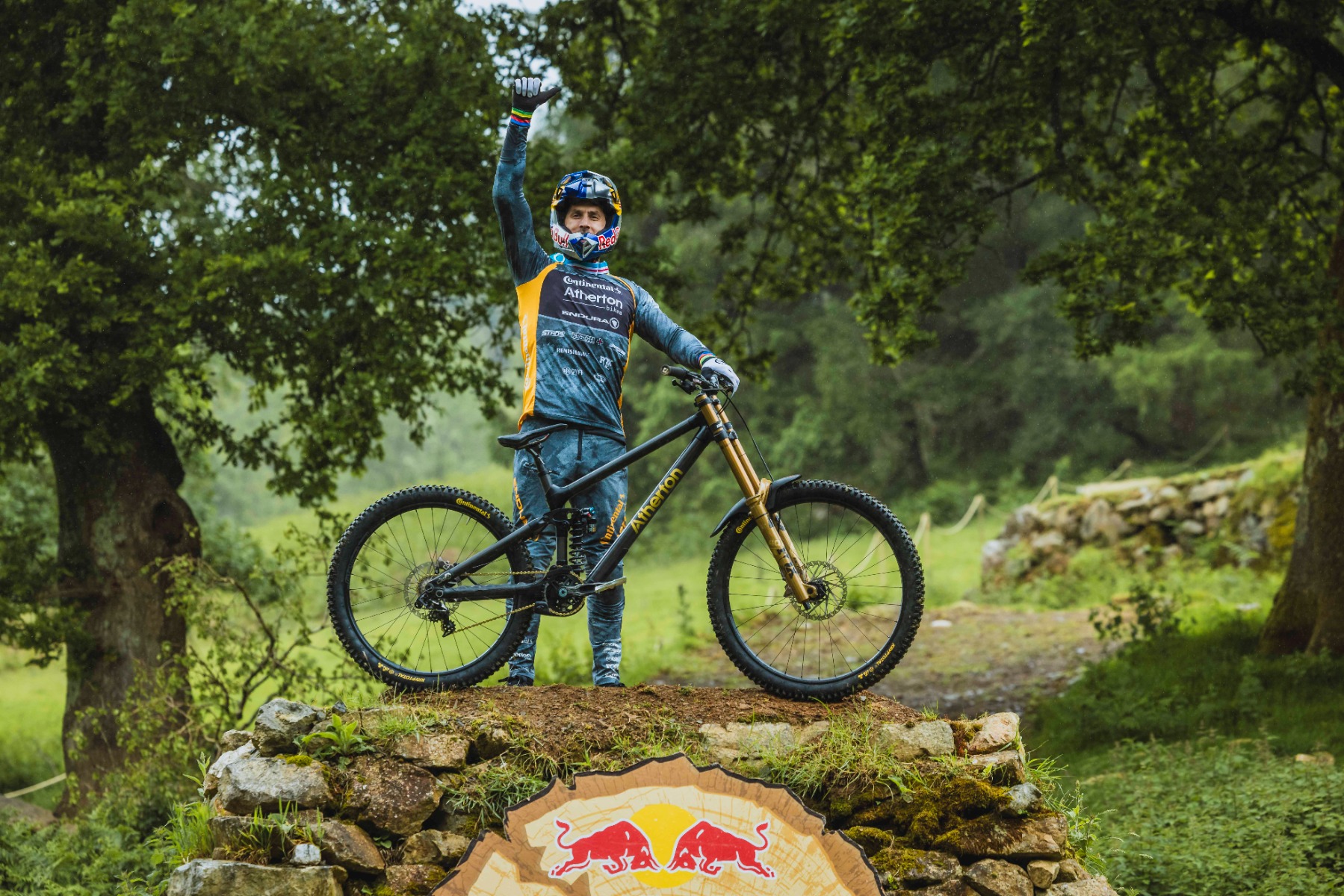
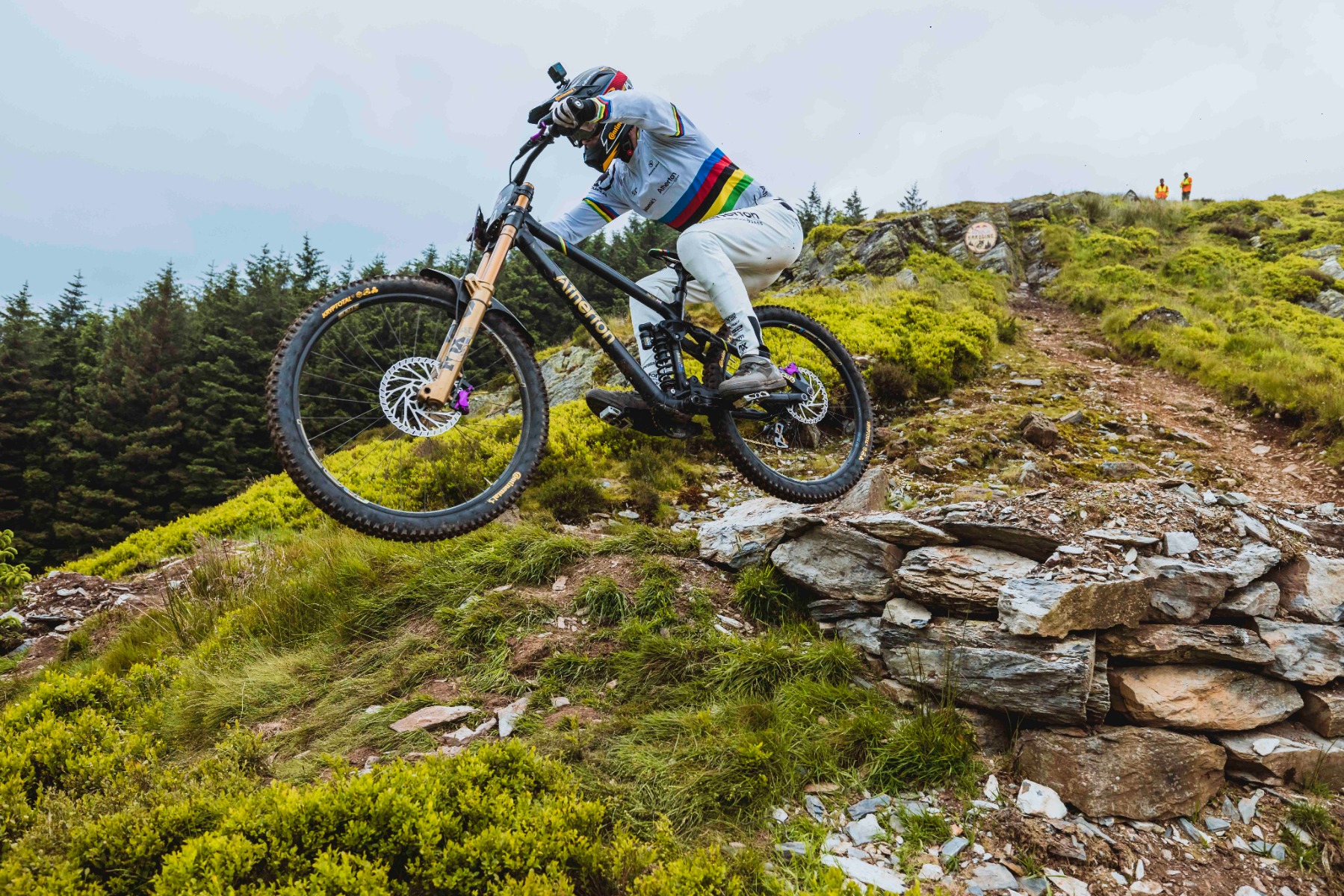
Marcus Schroder, EFBE
Marcus joined EFBE in 2012 after a "fairly usual career in mechanical engineering" he says.
“Cycling always was a hobby, but I have more of a road cycling background and nowadays find myself on a Gravel bike most often. I like to believe it’s more important to be a good engineer than to be a great rider, but that’s probably because my attempts at any technical MTB riding were so pathetic! I was just more comfortable climbing hills than going down. My colleagues Jens, who is Head of the Lab at EFBE, and Sascha, who is the Project Engineer here are competent Enduro and Downhill riders.“
We all believe that the EFBE Tri-test is the best lab representation of the actual intense use of modern high-end bikes. Whereas the safety standard for bicycles, ISO 4210, only knows one kind of MTB – which is, effectively, a 90’s XC bike – EFBE’s tests target specific use cases for all modern categories of MTB,
Marcus said “For instance, Category 5 DH use typically is quite demanding in terms of head tube loads representing a rider going downhill, but it does not consider that much intense pedalling. Category 4 (Enduro) goes a bit easier on the DH scenarios but considers more of the uphill. There is no indestructible bike – so if a part is pushed over the edge, maximum and overload tests ensure it fails safely."
For the Atherton bike, the demand was, right from the start, to combine both scenarios of our Tri-tests at their maximum intensities. That’s not a usual request but we’ve known this bike and some of the people behind it for a long time so it wasn’t a surprise to us".